Joint tracking systems for MIG/MAG Welding Robots.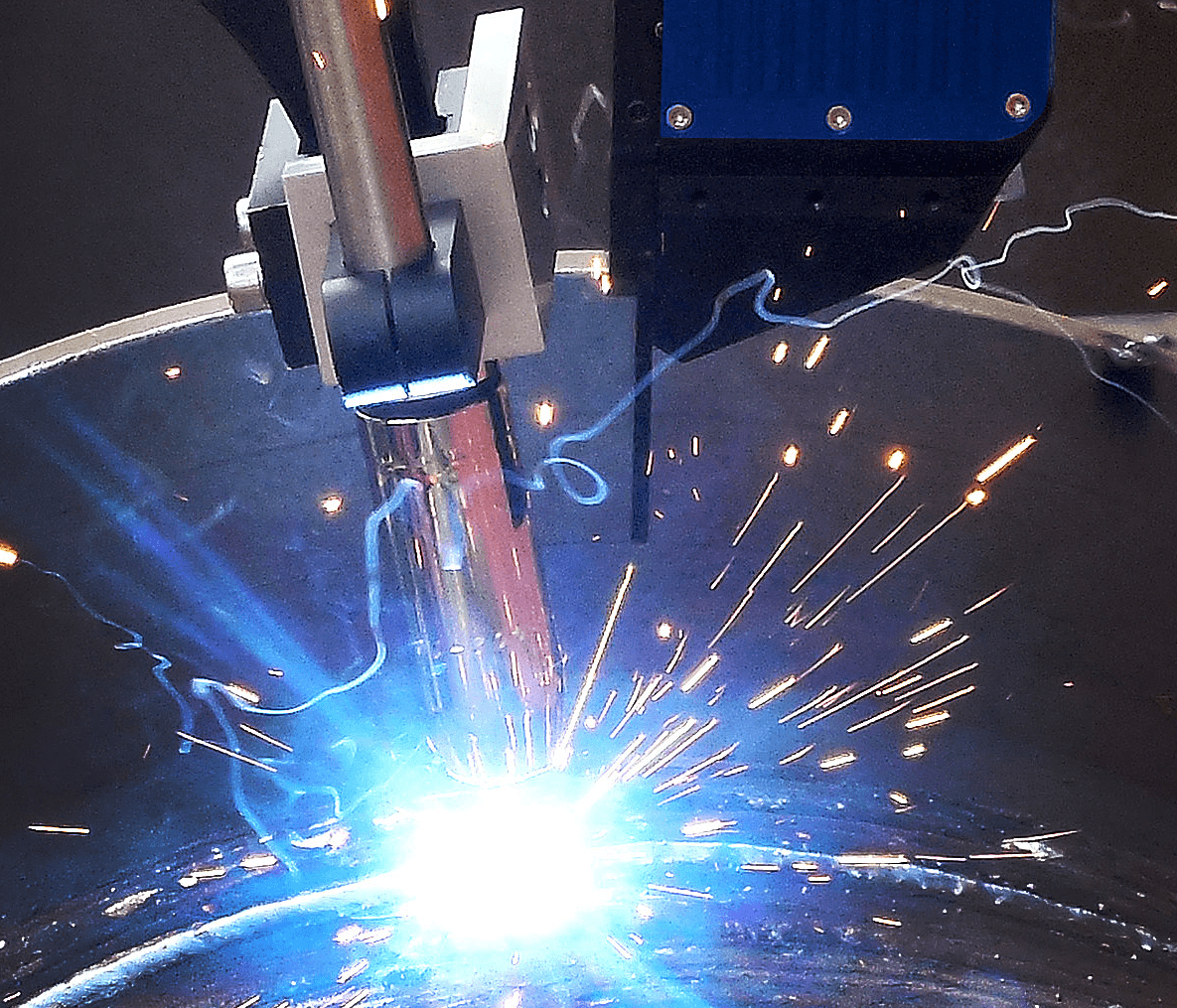
Robots don’t make mistakes when welding, but we make them indeed; for instance, placing pieces and their dispersion make robots lose their welding path, causing serious problems.
Currently, when we opt for a robotic welding cell in the hope of both to multiply by 3 production rates and reduce costs, we don’t tend to take into account that robots do not detect our errors: fixture design mistakes, arranging mistakes, dispersion of manufactured pieces and human mistakes when piece-feeding the robot. This translates into frustration for the production responsible when trying to meet with expected robot production targets.
The cost of a robotic welding cell is a key factor to consider. Robots integrators all too often omit to mention welding joint problems either because of ignorance or because of the possible price increase of adding a welding joint tracking system.
When designing the application, and trial tests are done, tooling is new, pieces are carefully placed and the welding torch is in good condition. Problems come when the system goes into the shop floor and production scrap rate is alarmingly high, far from targets.
SOLUTIONS FOR JOINT TRACKING
Most robot manufacturers have resolved these welding joint problems, under different commercial names, but same technologies at the end of the day.
These systems go from the cheapest and less precise one to the most sophisticated and accurate one, which is even able to visually-check welding joints with high-res cameras.
Seam Finding, measurement of the joint before welding:
- Touch Sense (tactital sensing)
- Laser Seam Finder (optical sensing)
- Laser Seam Finding Camera (optical sensing)
- 2D vision system (optical sensing
Seam Tracking, live weding joint tracking:
- Welding arc readings (tactital sensing)
- Laser Seam Tracking camera (optical sensing)
Seam Finding, measurement of the joint before welding
They measure the piece to weld and determine its position applying the new TCP values before the welding starts when it stops.
Touch Sense
It takes measures by touching the piece with either the welding wire or nozzle. When the piece is touched, an electrical circuit is looped and the position is registered, with a few measures, joint-position is determined. This is one of the most economical systems, but it has some limitations since it is not valid for systems with many welding joint dispersion where measures wouldn’t follow a normal distribution.
Benefits of this system:
- Low cost
- Feed wire has to be cutted
- It can detect V joints and olverap ones (the latter requires more time and referral points)
- Wire brake systems are recommended for narrow joints
- It can be easily programmed with macros
Laser Seam Finder
Laser measuring technology which is faster and more accurate than the previous method, althought they share the same working principles. No contact with the piece is required since the laser measures.
Benefits of this system:
- Faster and more accurate than touch Sense
- Low cost
- Avoids wire-cut
- It can detect V welding joints and olverap ones (the latter requires more time and referral points)
Laser Seam Finding Camera
A combination of a camera and a laser are used to take the measurements which are then triangulated. This method has some advantages over the two before described:
- It can work with any material and under any ligting condition.
- It detects very fast both the welding joint position and also its thickness.
2D vision systems: They are classical vision systems which detect changes on the piece position according to a 2D setup. These systems are used not only in welding but also in a considerable number of different applications.
Seam Tracking, live weding joint tracking
This system live-tracks welding joints, during the welding process and they adapt according to the data they get which indicates the joint position during the process.
Welding arc readings
During the welding joint process, if the distance to wire changes its welding parameters change too (i.e., voltange and working current) to adapto to the new position. This allows to have pre-established values and the robot changes its position to find them.
Benefits of this system:
- Convenient for materials with thickness greater than 8mm.
- Low cost
- Welding system inductance needs to be estimated.
- Allows multiple runs.
Laser Seam Tracking camera
It is the most complete system but also the most expensive one. It is able to read the joint during the welding process under any lighting condition and also any material. Its working principle relies on an HD camera adapted to the welding arc beam and a laser-light which is read by the camera. This makes possible to do a 3D read by triangulation. This system allows also to verify the welding joint once finished, thanks to its high-precision 3D measurement.
Jose Carlos M.
Share this article!
Contact the author for more info!